Efficient fulfillment practices are a must-have in today’s e-commerce landscape. In a Voxware survey, 69% of online shoppers said they’re less or much less likely to buy from a company again if their order doesn’t arrive within two days of the promised date. Order picking can be the most time-consuming part of the fulfillment process, yet accuracy is crucial.
You can’t trade speed for precision. However, a few best practices can boost your efficiency, making the picking process fast and correct
What Is Order Picking?
It is the process of gathering items from a warehouse to complete customer orders. It is the first step in order fulfillment. It is also one of the most expensive; research indicates it accounts for about 55% of the operating cost. Optimizing efficiency in this area can lead to savings.
How Does Picking Work?
Order pickers are responsible for retrieving purchased items and adding them to the shipment. They find the products shelved or stacked in the warehouse. They retrieve them by hand or using equipment such as a forklift. Then, they pass the order on to someone who packs them for shipping, or they may complete this step themselves.
What Are the Best Order Picking Methods?
The order picking process isn’t a one-size-fits-all system. Different methods exist, and choosing the most efficient one for your business depends on your product type, warehouse size, inventory amount, and number of employees.
Single-Order
Single-order picking is also known as discrete picking. It involves a worker completing one order at a time. It is the most common picking method; it works well for small warehouses with little space to cover. It also benefits new companies learning the order fulfillment process.
Workers may retrace their steps often during a shift, so it can be inefficient for large warehouses. However, it improves accuracy because employees focus all their attention on a single order at once.
Batch Picking
Pickers work on one order at a time with this method, also called multi-order picking. It decreases the workers’ travel time because they pull multiple items of the same type or SKU simultaneously. Companies that often receive numerous orders of the same item find batch-picking efficient.
Pick-and-Pass
Pick-and-pass fulfillment happens in warehouses divided into zones. Each picker chooses items for multiple orders within a zone, puts them in containers, and passes the container onto the next zone. Accuracy and accountability are two benefits of this method.
Zone Picking
Zone picking is similar to the pick-and-pass method. It divides warehouses into zones where workers pick items from their location and send them to the next zone. Zone picking benefits large companies with high warehouse order volumes because it prevents congested areas and helps with accountability.
Wave Picking
Wave picking involves all workers simultaneously picking orders from their zones instead of waiting for one zone to complete work and pass items along. By contrast, batch picking happens consecutively.
After the warehouse picking is complete, workers sort and consolidate orders into their respective shipping boxes. This method cuts down on picking time, but it may involve more workers.
Cluster Picking
Cluster picking allows pickers to fulfill multiple orders at once. Instead of focusing on similar items or SKUs, though, warehouse workers pick numerous items for multiple orders. Cluster picking often uses technology, such as carousels or mobile robots, to sort orders while reducing errors.
Goods-To-Person Picking
With this picking strategy, pickers remain at a workstation while automated equipment and conveyor belts bring the product to them. This system boosts efficiency by keeping people stationary and preventing congested areas.
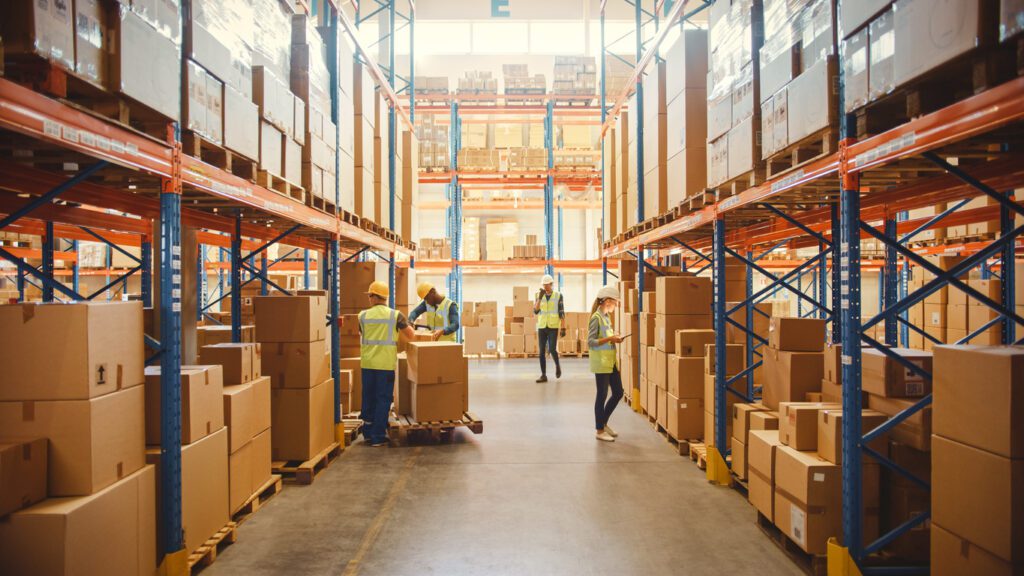
Finding the most efficient picking method can take some research and experimentation until you know what works. You may also need to change strategies when your business scales.
No matter which technique you choose for your warehouse, you have options to boost efficiency and help your production run as smoothly as possible.
1. Optimize Your Warehouse Layout
Your floor plan and organization are unique to your business. They rely on things such as:
- The type of products you stock (perishables, hazardous chemicals, shelf-stable items, etc.).
- Your warehouse size
- The volume you keep on hand.
- Equipment you use (forklifts, robots, conveyor belts, etc.)
A well-planned warehouse optimizes your internal and external spaces. Your design should create efficient movement, retrieval, and storage. As you plan your space, think about key areas, such as receiving, storage, packing, and shipping. Plan for office and break areas, too.
U-Shape
A U-shaped design has receiving and shipping on each end of the U, with storage and order picking in the back. This plan can work well if the receiving and shipping bays allow enough room for trucks. It’s an efficient design for small spaces.
L-Shape
An L-shaped design puts receiving and shipping at each end of the L, with a small storage area in the corner. If you implement cross-docking and store products for a short time, this design may create efficiency for you.
I-Shape
Businesses with high-volume orders may like an I-shape layout. Receiving, storage, and shipping fall into a straight line. This design reduces back-and-forth order picking to avoid bottlenecks.
2. Designate a Receiving Process
Items that wait on the receiving dock are more or less dead weight. They still need to be counted as inventory, so they are unavailable to customers. Allowing them to linger can cause long lead times and order delays.
A standard receiving procedure can alleviate this pressure point.
Documentation
Send suppliers your packaging requirements, including sizes and weights, number of items per carton, number of packages per pallet, and labeling information. A standard warehouse receiving order can outline your criteria.
Unloading and Receiving Products
Your receiving team should meet the shipment provider to receive and unload cargo, checking orders to ensure everything is correct before signing off on the delivery notice.
Inventory Counting and Inspecting
Suppose the receiving team finds discrepancies after the shipment provider has left. In that case, they should contact the provider as soon as possible. The team should inspect the products, look for damage, and ensure correct product codes. Everything should match the warehouse receiving order.
Storing Inventory
Once the products meet all criteria, they can be transferred to the storage area, ready for order picking.
3. Use Automated Picking Systems
Traditional picking methods relied on paper lists. Today, technology provides several automated techniques that can increase picking efficiency.
Voice Picking
Pickers wear a headset connected to an order management system to use this automated method. The system tells them where to find the items in the warehouse. Voice picking can speed up travel time and improve accuracy.
Mobile Scanning
Each warehouse item has a unique barcode for the mobile scanning system. A mobile scanner displays an order’s picklist and the items’ locations. The scanner has an error-checking system that notifies the picker if an item doesn’t belong. Mobile scanning is an excellent method for increasing order picking accuracy.
Pick-To-Light
LEDs throughout the racks and shelves correspond with a barcode scanner in the pick-to-light system. The picker has a barcode with information on a single order. The barcode is usually on a shipping container.
When the picker scans the barcode, it activates LED lights near the products. The picker follows the lights to find the products. Pick-to-light technology creates efficiency by speeding travel times and boosting accuracy.
Vision Picking
Vision picking harnesses the power of virtual reality. The picker wears a headset with an integrated camera, wearable computer, and control software. The device connects to the warehouse management system. The navigation system shows the picker the most efficient route and the item’s exact location. The system provides visual verification. Vision picking increases efficiency and accuracy by outlining the steps for order picking.
4. Keep the Warehouse Clean and Organized
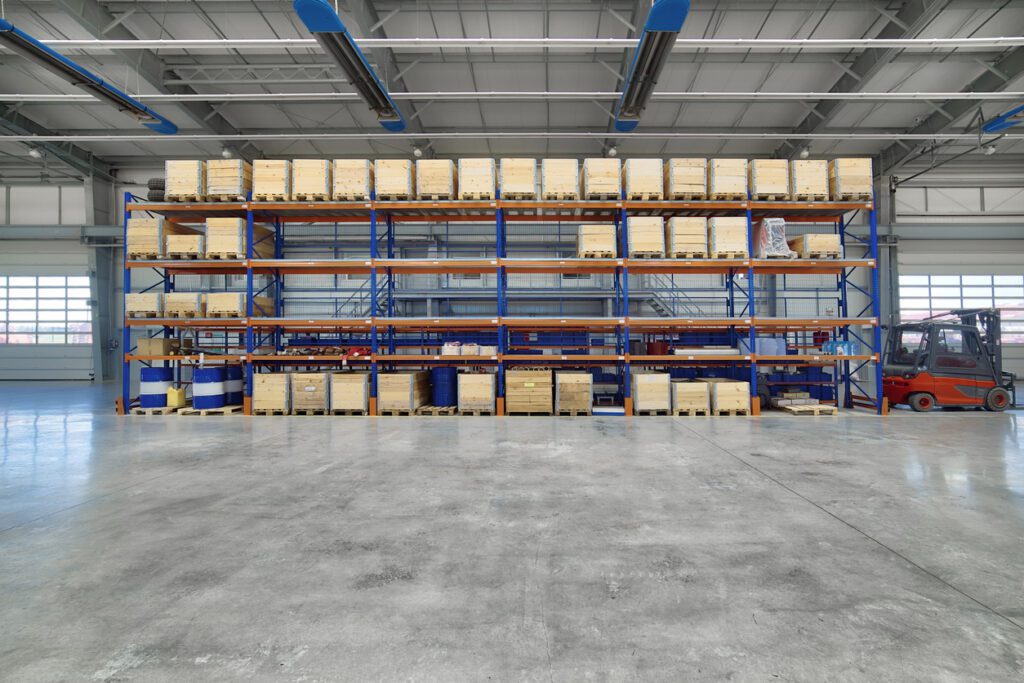
While this step may seem more like housekeeping than an efficiency boost, a clutter-free warehouse is essential to productivity. An organized, clean warehouse provides benefits such as:
- A professional appearance
- Compliance with health and safety mandates.
- Increase employee morale
- Decreased maintenance costs
Scientific research connects good air quality, reduced noise levels, and proper lighting to increased worker productivity and efficiency.
Keep Workspaces Free From Dust, Spills, and Debris
Whether employees take charge of sweeping and organizing their areas at the end of the shift or a cleaning service does this, the step ensures the warehouse stays clean and organized. Boxes and packing materials create distractions and slip-and-fall hazards.
Label Items and Work Zones
Ensure workers know where everything belongs by providing adequate labels. Outline the work zone with signage. These steps are especially critical if you use temporary workers or have high turnover. Signage increases order picking efficiency by saving workers from searching for zones or products.
Use Just-In-Time Inventory Practices
The less product you store, the easier it is to keep your warehouse organized. Just-in-time inventory management frees up valuable space and prevents waste. You can still plan for safety stock to avoid shortages, but keep it in a designated area and rely on your data to hold the right amount.
Classify Inventory Into Slow- and Fast-Moving Categories
Take stock of the products in the warehouse and categorize them by picking frequency. Frequently picked items should be easy to find and reach while slower-moving inventory can go toward the back.
5. Manage the Returns Process
Returns management is essential to customer satisfaction. It is also important in warehouse efficiency. Your returns processing team can benefit from a designated space to receive, unpack, and inspect products. The team can then enter the products back into your stock for order picking or package them again for various channels, including:
- Resale
- Repair
- Return to supplier
- Recycling
A solid warehouse management system can help you optimize the returns process. An automated WMS system with handheld scanners lets employees collect package label information such as SKUs, UPCs, and RMA numbers. The information is then uploaded to a real-time inventory management database.
Build Customer Satisfaction Through Returns
While getting undamaged products back into inventory is essential, sending the information to accounting as quickly as possible is vital. The sooner the accounting department can process the return, the more satisfied the customer will be.
Product returns are inevitable. Rather than viewing them through a negative lens, use them as an opportunity to build customer trust — complete the process quickly and get their money back to them. While the warehouse might not have direct contact with customers, it is just as vital to making a favorable impression.
Returns also provide a chance to improve warehouse logistics. As an example, are customers returning orders because they received the wrong item? If so, it may point to a warehouse picking process issue.
6. Use a Perpetual Inventory Strategy
Perpetual inventory involves checking stock levels in real time as they enter and leave the facility. It is an automated process that prevents shortages and aids in categorizing items. The software automatically logs picking, shipments, and receipts. These strategies help you optimize storage and improve warehouse flow.
Perpetual inventory uses technology such as:
- Weight sensors on storage locations, load carriers, or containers.
- An RFID system that can record multiple items in bulk, even over long distances.
- Video systems that scan and locate data.
These systems integrate with warehouse management software to provide constant updates. Perpetual inventory methods help order picking in warehouses with multiple SKUs by preventing stockouts.
7. Establish KPIs
Measuring your key performance indicators is an essential warehouse management procedure. Your KPIs will help you identify what you’re doing most efficiently and what needs work.
Supplier On-Time Rates
Your efficiency depends in part on your suppliers. Monitor them to make sure they reach benchmarks for timeliness. Otherwise, you won’t be able to stick to your customer delivery times.
Dock-to-Stock Time
Dock-to-stock time is the amount of time between when a shipment reaches your receiving area and when it goes on the shelves for order picking. A timely dock-to-stock process keeps your receiving area clear and ensures products are ready to sell.
Picking Accuracy
The goal of any picking process is 100% accuracy. Inaccurate orders lead to customer complaints and returns. Knowing your accuracy percentage helps you identify problem areas and make adjustments or corrections.
Internal Order Cycle Time
This KPI shows how long it takes to complete an order. It begins when the customer purchases the product and ends when it leaves the shipping area. Internal order cycle time helps you plan for increases and decreases in product demand (which can really help if you have seasonal products). It also demonstrates the speed of order picking.
Space Utilization
Space utilization helps you optimize your storage area. It keeps you from stocking too much inventory and draining your budget or too little inventory, causing fulfillment delays.
On-Time Ready To Ship
This key performance indicator shows you the percentage of orders that meet the shipping schedule. It helps you evaluate the fulfillment process as a whole and streamline your processes.
8. Improve Travel Times
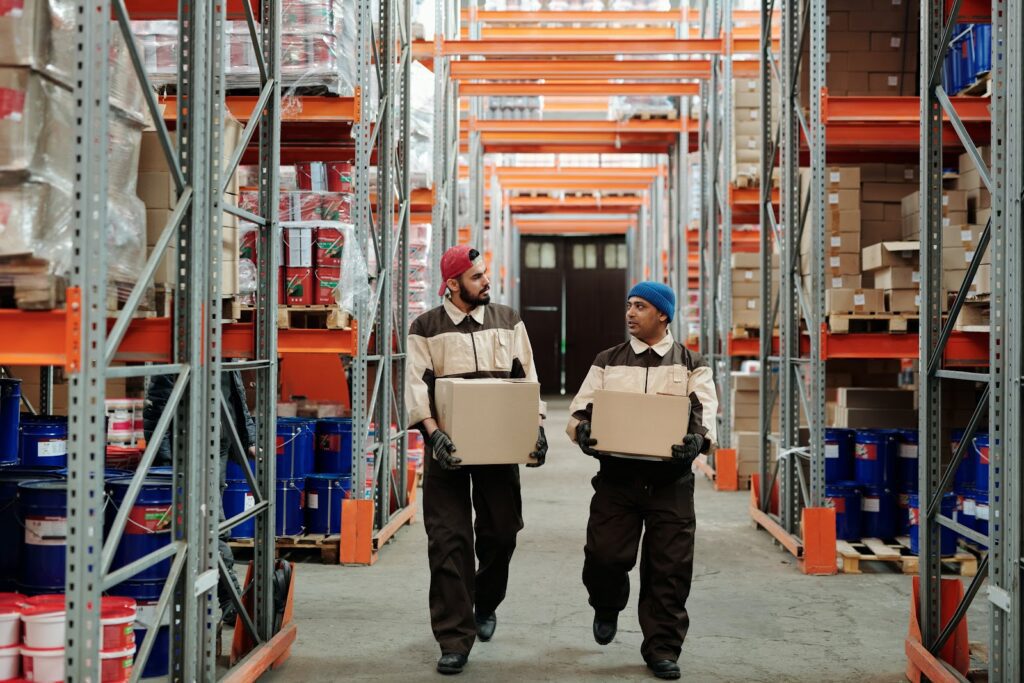
Your order picking and warehouse layout strategies can help you reduce travel times. However, you probably have things you can’t alter. Even the most efficient layout comes with constraints (such as building size and shape). You may have to get creative to decrease travel amounts.
Arrange the Inventory To Reduce Travel
Do you have items frequently picked together? Try slotting them — group them next to each other to save pickers from repeatedly covering the same ground to retrieve them.
Popular items should be front and center (or wherever is most manageable to reach). Inventory that sells less frequently should be stored in the back.
Use all the vertical space you can. Mezzanines, overhead conveyors, and automated storage and retrieval systems help with this approach.
A mobile power workstation allows employees to bring technology with them. Instead of walking from a desktop computer to the printer or walking to retrieve a scanner, they take the workstation with them and keep tools at their fingertips.
9. Focus on Ergonomics
A safe, comfortable workspace ensures pickers work at their highest efficiency level. According to OSHA, musculoskeletal stress is an order picking occupational hazard. It happens when employees bend, twist, reach, and lift heavy items.
Ergonomic Best Practices
Provide workers with safety equipment such as gloves, earplugs, and containers with handholds. Ensure walking surfaces are not slippery. Break heavy loads into smaller, lighter ones when possible. Encourage pickers to work in teams to lift heavy boxes.
Additionally, enforce break times and job rotation to ensure employees get well-deserved rest. Adequate break times are not idle times — they increase efficiency in the long run.
Other basic ergonomic steps include:
- Providing cushioned mats where employees stand for long periods.
- Training pickers on proper bending and lifting techniques.
- Moving popular inventory to a waist-high level (the “power zone“) to reduce stooping or reaching.
- Using equipment such as forklifts, robots, and stock-picking machines to aid employees.
- Ensuring the picking route is well-lit and free of clutter or objects.
Using the most efficient picking method boosts workplace ergonomics. It reduces the amount of walking, reaching, and lifting employees do while order picking by decreasing travel time.
A goods-to-person strategy eliminates much of the lifting and bending required with other methods.
10. Organize Around Seasonal Demand
Even though seasonal demand is predictable, it often sneaks up on warehouse managers. Some companies rely on the income it provides, while it’s a nice boost for others. No matter your seasonal demand level, it’s crucial to plan for it and organize your warehouse to maintain efficiency.
Determine Season Length and Sales Volume
First, you need to know what products move faster during the peak season and how long the demand lasts. Look through sales trends to determine percentages.
Shorten Lead Times for Seasonal Products
Decreasing your lead times for seasonal products is a must to maintain efficiency. You may need to update your inventory management system, hire additional workers for order picking, or allocate tasks differently during the peak season.
Expect Variations From Previous Seasons
Unless you have a crystal ball, you cannot pinpoint seasonal demand with perfect accuracy. A contingency plan helps you prepare for deviations. Consider what actions to take if sales suddenly scale or if overall demand fluctuates from previous years.
Budget for Labor and Materials
Scrambling to find resources for extra expenses can dent your efficiency. Budget for seasonal expenses such as extra labor, overtime, additional products, and more shipping supplies. The peak season is busy enough — you don’t need surprises.
11. Empower Team Members
Emphasize to your pickers that their input is vital to creating an efficient warehouse. Order picking is a complex strategy that relies on the skills and knowledge of those completing the task. Engage them often to prevent or reduce top-down directives.
Review Processes
Meet with team members to go over procedures, identify what works best in your warehouse, and repair bottlenecks. Employees need to know they can share ideas and suggest improved strategies.
Ask for Feedback
Rely on your pickers to tell you about the methods that create efficiency. Ask for their suggestions on process improvements. While some workers may hesitate to initiate a conversation, asking them can encourage them to share ideas.
Help Staff Learn New Technologies
Implementing new automation or software can be daunting. Order picking employees may worry that their jobs are in danger — what if the new systems eliminate their position? What if they can’t keep up? Reduce their concerns with transparent communication and thorough training.
Provide Safety Training
Because safety and efficiency go together, keeping pickers trained on current safety protocols is essential. Safety training also reinforces the importance of using the proper equipment, protective devices, and materials handling methods.
Reinforce a Culture of Open Communication
Recognize and reward employees who share ideas. These strategies demonstrate your willingness to follow through. They show pickers you mean what you say when you ask for their ideas.
12. Use Multiple Picking Methods
Order picking is a dynamic process. If one method isn’t working, try another. You can also combine methods.
Zone-Batch Picking
Pickers work within a zone but do batch picking within that zone. Batches group together similar orders to reduce travel time and increase speed.
Zone-Wave Picking
Workers stay in a zone and are responsible for picking SKUs for all the orders in their zone. They remain within the single scheduled time slot for their shift.
Zone-Batch-Wave Picking
Each picker retrieves all the products for orders in their designated zone. They pick products simultaneously. Each shift uses multiple time slots; workers fulfill orders in a set scheduling window.
Work With an Experienced Fulfillment Company for Efficient Order Picking
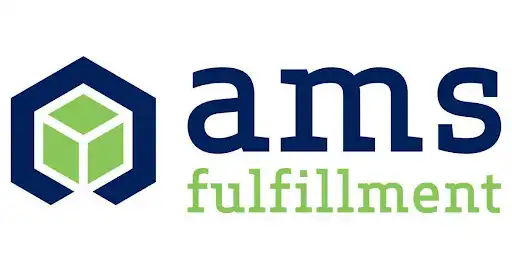
You can increase efficiency by working with an experienced partner. AMS Fulfillment can help you grow your business by aiding you with order pricing, product distribution, and increasing sales. At AMS, we understand the value efficient order picking adds to warehouse success. Collaborate with a knowledgeable partner today — contact AMS for your fulfillment solutions.